What is the difference between a servo thermoforming machine and an ordinary thermoforming machine?
1. Accurate energy control and fast response The pressure energy can be pre-set simply and accurately, and accurate and precise pressure without discrepancy is repeatedly implemented in each stroke to ensure the uniformity of the product. Servo motor direct drive, no clutch response time, fast running response. 3. The molding speed is fast, extending the life of the mold When the screw press is close to the bottom dead center, the slider speed is extremely fast, and the time for the die to extrude the material is very short, and the processing can be completed instantly before the hot material cools. The contact time with the mold is short, and the mold temperature changes little, which greatly prolongs the life of the mold. 5. The energy process can be controlled at will, with a wide range of applications The servo CNC press can set the pressure energy, so that the slider first accelerates and descends, and then decelerates to pressurize the material with the set energy. Large tonnage presses can also forge small parts, and the processing time per unit stroke is basically unchanged. Use both size and size, with a multiplier effect. 7. Stamping forming, high pressure energy The pressurization method is the same as the conventional friction press, the flywheel energy is completely consumed and pressurized, and it is an instantaneous press pressurization method, so the generated pressurization energy is very high. 2. Reasonable structure, more uniform products Since there is no structural bottom dead center, there is no need to worry about excessive loads due to oversized materials or uneven heating temperatures, as well as slip jams (seize stops due to overload). Moreover, the same material can be repeatedly pressurized with different strengths to gradually deform, and successively forging is carried out. 4. Simple structure, low maintenance cost Servo motor direct drive, simple structure and less parts, low maintenance and maintenance costs. In normal operation, the motor itself stops the slide without the need for a brake. The mechanical brake is only used for double protection and is used in emergencies such as power outages, and the service life of the brake pads is extremely long. 6. High efficiency, energy saving, lower production cost The servo motor only turns when the machine is on, (the friction method is that the motor runs continuously). The comprehensive energy saving effect saves about 55% energy compared with the previous friction press. 8. Low noise, low vibration Pressure is produced within the frame. Compared with the punch hammer, there is no excessive ground vibration, and the ground foundation work can be carried out inexpensively. Noise and vibration are far lower than impact hammers.
Detailed explanation of the production process of disposable plastic cups
1. Install the mold and prepare the material Install the mold on the plastic cup making machine; Use a sheet machine to make new plastic PP pellets into sheets and roll them into a barrel. 2. Turn on the cup making machine and produce The sheet is loaded into the feeding place of the plastic cup making machine, the oven is heated, the sheet is fed, and the production starts. Three, packaging, color printing After the market cups are stacked using a cup stacking machine, they are packaged; The supermarket cups are automatically nested by the cup stacking machine and then fed into the packaging machine for automatic bagging; Boxes, products that cannot be used with a cup stacking machine, use a manipulator to suck out the products, stack them, and pack them into boxes; The color printing cups that need to be printed are input into the color printing machine for printing. 4. Remaining material processing, pulling tabs, recycling production The leftover material produced in the production is put into the pulverizer to be processed into granules, and then mixed with the new material, and then put into the sheet machine to pull the sheet. Here you can use an automatic feeder to save manpower. V. Summary In fact, the production process is very simple, that is, pulling, producing, processing leftovers and then pulling, producing, and so on. The configuration of the machine on demand, including the model size, how many units, and how many kinds, are arranged according to the actual production needs. Among them, the cup stacking machine, packaging machine, manipulator and feeding machine are not necessary to save labor, improve efficiency, reduce costs and hygiene considerations. At the same time, automated production is the current trend, and reducing costs means improving competitiveness.
What should be paid attention to when using the sheet machine?
1. From the feeding section to the connection between the barrel and the forming die, the temperature of each section of the barrel of the sheet machine is different, and the temperature gradually increases. 2. The temperature of the forming die should be slightly higher than that of the cylinder. In general, the temperature difference should be controlled between 5-10 °C, and the temperature at both ends of the mold is also slightly higher than the middle temperature. The temperature difference is the same as before. 3. The height of the three-roller intermediate roller is on a plane with the lower lip of the mold, and the lip end face is parallel to the intermediate roller. 4. In order to make the melt form a uniform thickness in the mold, the temperature of the forming mold should be kept at a certain temperature value. 5. In order to avoid affecting the thickness of the sheet, the working temperature of the three-roller of the sheet machine should be higher than the speed of the sheet extrusion die, and the speed should be stable.
How does the sheet machine operate?
How does the sheet machine operate? Categories:Industry News Author: Origin: Time of issue:2022-06-02 1. If the sheet machine is put into use for the first time, when turning on the machine, we should first heat the machine for about 40 or 50 minutes. The recommended operation method is to pull the V-belts of the motor by hand until they are free; continuously pull 8-10 times according to the normal working direction, then continue to heat for about 10 minutes, and then start, but due to the need for continuous supplementary heat for normal production, the heating should be continued. ; Adjust different temperatures according to the different properties of plastics. 2. When working, it is necessary to ensure the temperature of the machine, not high and low. 3. The feeding of the sheet extruder should be uniform and add enough material. The feed rate and feed rate of the sheet extruder would otherwise affect pellet quality and yield. 4. The power supply of the sheet machine should be completely cut off when it is stopped.
Mechanical use of multilayer sheets
Multi-layer co-extrusion sheet machine can produce various PP, PE, PS, HIPS and other multi-layer composite plastic sheets according to different uses and characteristics. Its products are widely used in-disposable beverage cups, jelly cups, packaging bowls, snack boxes, packaging boxes and other products.
Advantages of horizontal multi-layer co-extrusion sheet machine
Unit advantages: 1. Precision multi-layer distributor, using flow ratio and flow area ratio variable adjustment technology, layering more uniform. 2. Roller independent power linkage, linear speed can be synchronized control. 3. The whole machine adopts PLC control to realize automatic control of parameter setting, feedback, alarm and other functions 4. The screw and barrel are made of high-quality alloy steel materials, and are nitrided to ensure the surface Hardness and machining accuracy; 5, the use of rapid hydraulic network change device, high production efficiency; 6. The distributor and T-type die have reasonable structure, advanced flow channels, and stable and insoluble shunting of each layer, Adjustable thickness; 7. The three rollers adopt horizontal structure to make the sheet production process more reasonable and improve the quality of sheet products
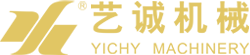
The company's leading products are (degradable material) sheet extrusion units,high-speed automatic hydraulic(Servo) forming machine, mold professional customization and automatic auxiliary equipment in the forming machine production line, such as manipulators, automatic counting and packaging machines, automatic cup stacking machine, (online) crusher, mixer, raw material feeding machine, etc.
Product classification
Contact Us
Telephone: +86-754-88213996
E-mail : root@stycjx.com
Fax: 0754- 88212991
WeChat: 138-2965-1950
Add:
NO.1/1, XinLong East Road, TuoLian Street, JinPing District,
ShanTou city ,GuangDong,China.
©2023Guangdong Yichy Technology Co., Ltd.